You can see the oil samples and online particle count readings below:
Before Filtration After Filtration Initial Reading Final Reading
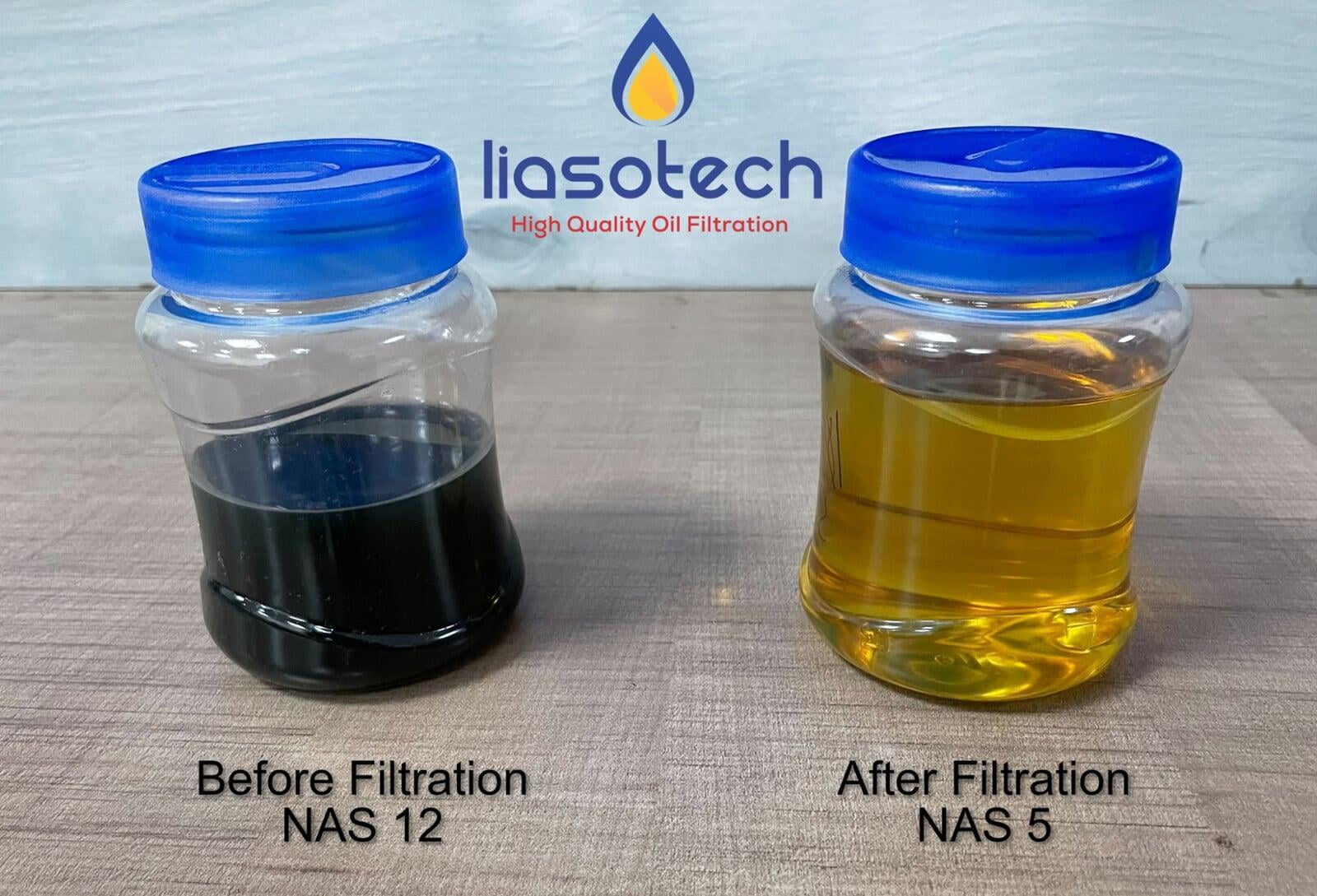
Liasotech conducted a successful oil cleaning demonstration at one of our customer's sites in the Plastic industry. This demonstration was crucial for the customer, who had previously faced multiple failures with other filtration companies in their attempts to clean hydraulic oil to the required standards.
Problem
Upon initial assessment, the hydraulic oil was tested and found to have a cleanliness level of NAS >12. This was significantly higher than the system's requirement of NAS 5. The excessive contamination in the hydraulic oil posed a serious risk to the machinery's performance and longevity, necessitating immediate and effective intervention.
Solution
In response to the customer's challenge, Liasotech deployed a skilled service engineer to the site for an initial assessment. Upon testing, it was confirmed that the hydraulic oil's cleanliness level was indeed at NAS 12. To address this, we installed a 12 LPM oil filtration machine equipped with 3-micron filters, all under the supervision of our service engineer. The filtration process commenced and continued non-stop for approximately 48 hours.
Result
The outcome of our intervention was highly successful. The filtration system reduced the oil's cleanliness level from NAS 12 to the desired NAS 5, meeting the stringent requirements of the customer's molding equipment. This significant improvement demonstrated the effectiveness of Liasotech’s technology and expertise in oil filtration.
Benefits
The successful filtration of the hydraulic oil brought multiple benefits to the customer. Firstly, achieving NAS 5 ensured the optimal performance and longevity of their equipment, reducing the risk of breakdowns and maintenance costs. Secondly, the customer, impressed by the results, expressed their interest in placing more orders. This not only solved their immediate problem but also paved the way for a long-term partnership with Liasotech, ensuring sustained equipment efficiency and reliability.
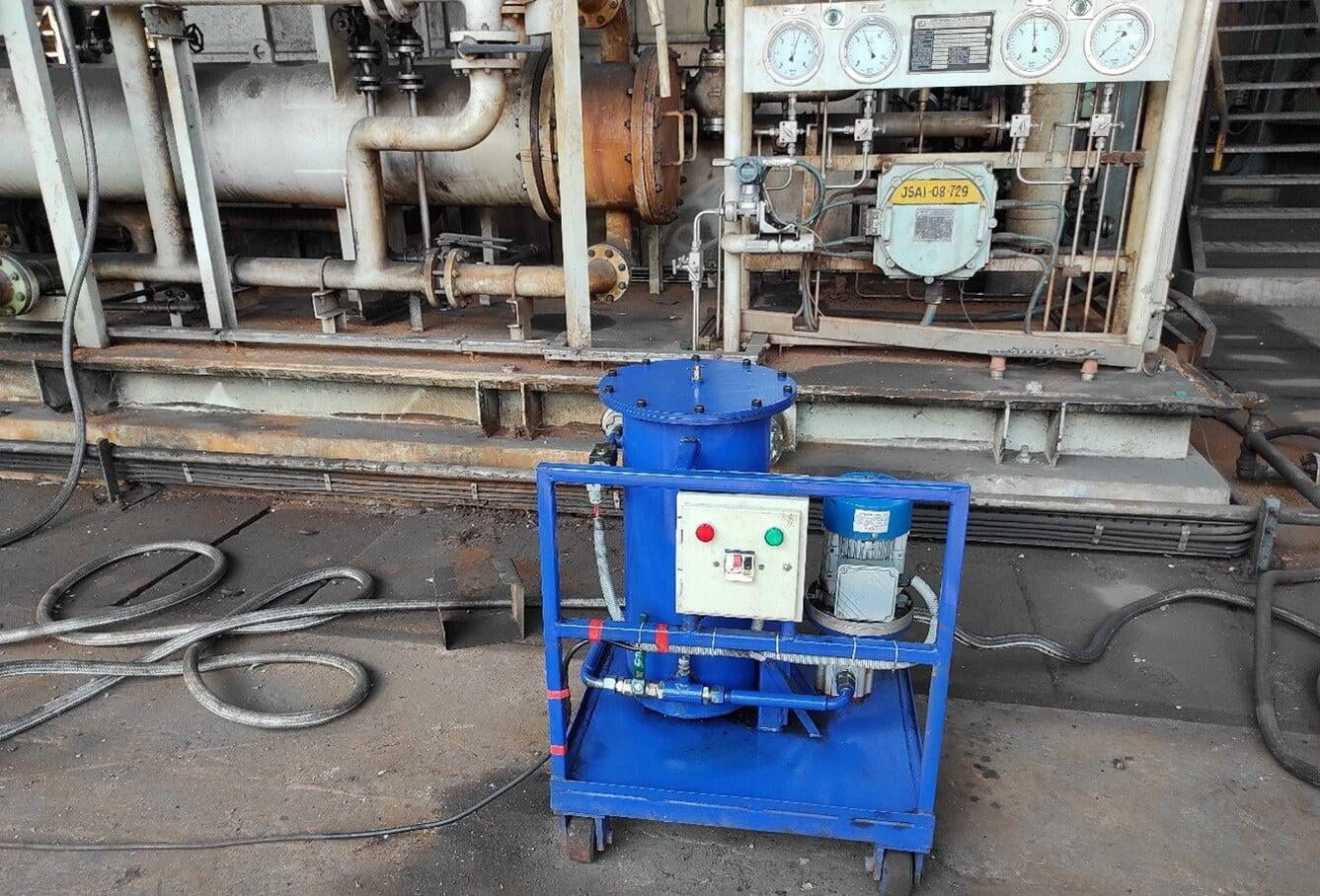
The Problem
An integrated steel plant in Odisha faced a significant challenge in maintaining oil cleanliness within one of its hydraulic systems, which has a 3000 liter tank capacity. Despite operating an ELC filtration machine continuously 24/7, the plant consistently recorded high particle count readings at NAS 10 or higher. Such high contamination levels posed a risk to the efficiency and longevity of the hydraulic system, making it critical to find a more effective solution to ensure system reliability and performance.
The Solution
To address the contamination issue, the plant official decided to replace the ELC filtration machine with our Hydraulic Oil Filtration System (HOFS-16). The HOFS-16 system was equipped with our finest 3-micron absolute filter elements, specifically chosen to eliminate particulate contamination in the hydraulic system effectively.
The Results
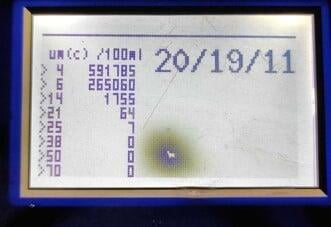
Initial Particle Count Reading - 09:30AM
The initial measurement taken at 9:30 am showed a particle count of 20/19/11, equivalent to NAS Class 10. This level of contamination was considerably high and unsuitable for the hydraulic system's optimal performance.
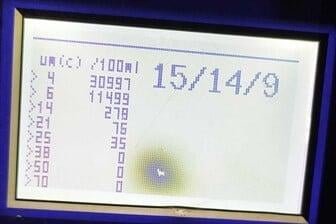
Final Particle Count Reading - 05:30PM
After operating the HOFS-16 filtration system throughout the day, a subsequent particle count reading was taken at 5:30 pm. The reading showed a significantly reduced particle count of 15/14/09, equivalent to NAS Class 5. This indicated a much cleaner state of the hydraulic oil, well within acceptable levels for such systems.
The Benefits:
Implementing the HOFS-16 filtration system brought several advantages:
The significant reduction in particulate contamination improved the hydraulic system's reliability and operational efficiency.
Cleaner oil helps reduce wear and tear on system components, extending their lifespan.
With lower contamination levels, the frequency of maintenance and associated downtime decreases, leading to cost savings.
Maintaining cleaner oil enhances the overall performance of the hydraulic system, contributing to smoother operations and improved productivity for the steel plant.
Problem Statement:
A cement plant in Andhra Pradesh had invested on an industrial oil filtration system from another manufacturer. Despite the cost and claimed benefits, they continued to face:
Failure to achieve the target NAS 5 cleanliness level, even after months of use.
Increased maintenance issues with hydraulic and lubrication systems.
Frequent machine downtimes and repairs.
This caused concern among the maintenance and operations teams, who had anticipated improved performance and cost efficiency.
Solution:
After understanding the challenges, we recommended our Advanced Oil Filtration System, designed specifically for critical equipment in dust-prone, high-temperature industries like cement.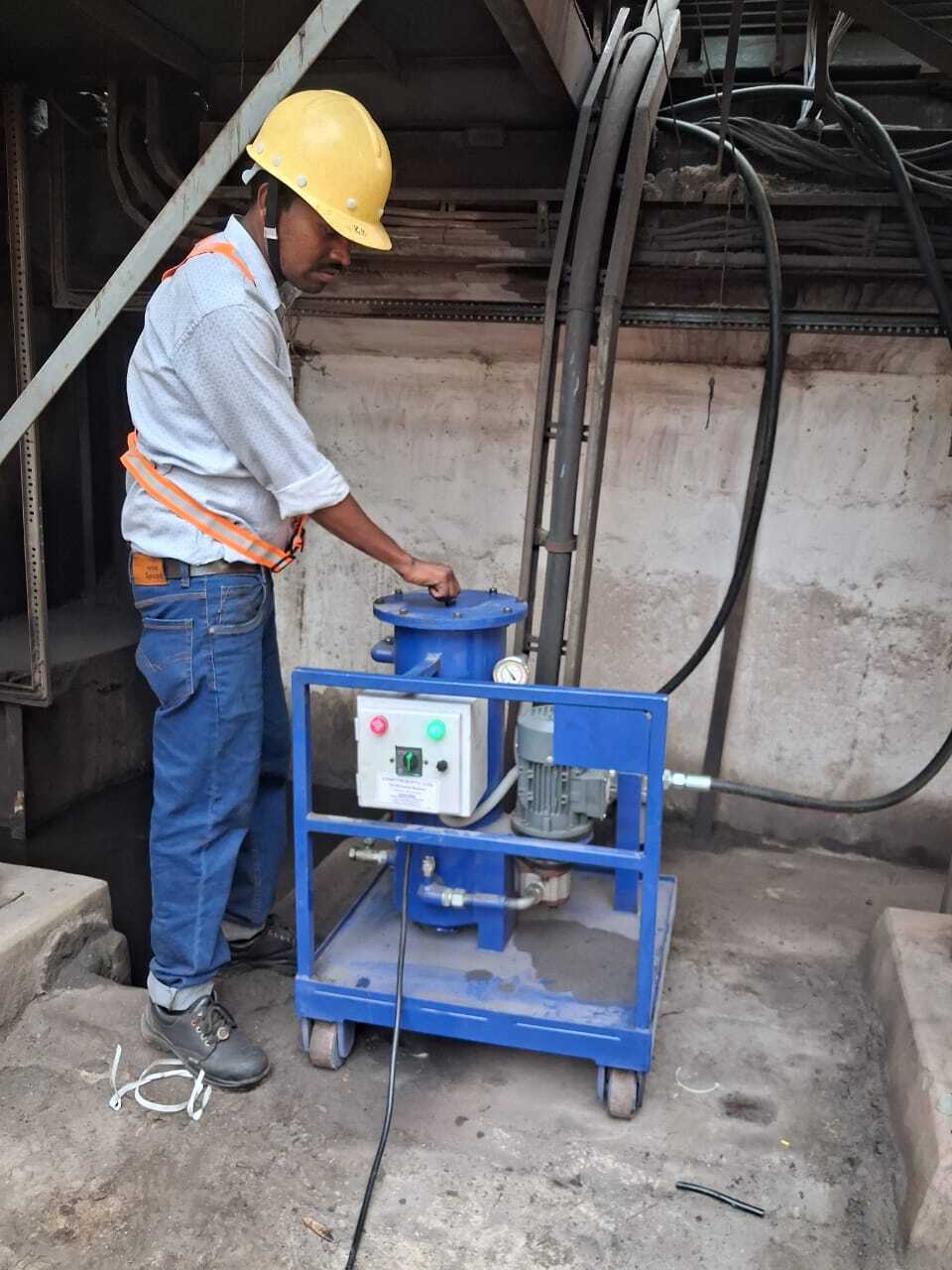
Implementation Highlights:
Installed a customized filtration unit compatible with their systems.
Provided on-site technical support for installation and training.
Ran continuous filtration in offline mode, allowing uninterrupted plant operation.
Started regular oil analysis to track progress.
Results
Within a short time frame of 48 hours of continuous filtration, the results were clear:
Oil cleanliness improved from NAS 11 to NAS 4
No replacement of oil was required, which helped them recover losses from their earlier investment.
The maintenance team reported noticeable improvement in equipment reliability and smoother operation.
Benefits:
a) Achieved NAS 5 Cleanliness, improving oil and machine health.
b) Reduced Maintenance Costs: Less component wear and longer oil life.
c) Avoided Costly Oil Replacement.
d)️ Enhanced Machine Uptime in a harsh cement plant environment.
e) Restored Trust in oil filtration solutions after a disappointing experience with a prior vendor.
The Problem
A ductile iron pipe manufacturer in West Bengal faced a serious challenge in their plant's hydraulic system.
The plant had already invested in a few number of oil filtration machines. But within just a few months, the Filtration Systems became ineffective, failing to deliver results. Concerned, they began searching for alternatives and that’s when they discovered Liasotech’s hydraulic oil filtration solutions through our website.
When we engaged with their maintenance team and reviewed their oil analysis reports, the root cause became clear:
Oil contamination ranging from NAS 9-12 in various systems, far above acceptable safety limits.
The plant officials explained that:
- Valves in the hydraulic presses were choked frequently.
- Movements became erratic : too slow, too fast, or stuck halfway.
- On the finishing tables, pipes were getting damaged due to delayed valve responses.
Machine cycles were becoming inconsistent, creating production losses and quality concerns
The Solution
Liasotech Oil Filtration System was then connected to their hydraulic press setup and the first baseline NAS reading was recorded: NAS 10.
We ran continuous offline filtration for 12-14 hours. Once the cycle completed, the new oil report showed: Solid contamination reduced to NAS 5
The Final Verdict:
Problem: Moisture Contamination issue in a Power Generation Company in Gujarat
A leading power plant in Gujarat was facing recurring challenges due to moisture contamination in their hydraulic systems. Despite routine maintenance, they experienced:
Hydraulic failures that delayed production and delivery timelines.
System inefficiencies due to reduced lubrication properties
The operations manager noted,
“Even with regular filtration, we couldn’t remove the dissolved moisture and we kept seeing equipment wear.”
Solution: Deploying Liasotech's Vacuum Dehydrator System (VDS)
While exploring advanced solutions, the team discovered Liasotech’s Vacuum Dehydration System (VDS) :: a system specifically engineered to remove free, emulsified, and dissolved water from hydraulic oils.
After installation, the results were immediate and measurable for 2 systems:
Mill | Oil Quality before VDS machine installation | VDS Installation Date & Time | VDS Machine Removal Date & Time | Total Time taken for moisture removal | Final Oil Quality |
A | Moisture – 600 PPM | 26.03.25 | 28.03.25 | 34 hours | Moisture – 90 PPM |
B | Moisture – 157 PPM | 04.04.25 | 05.04.25 | 18 hours | Moisture – 87 PPM |
In a few weeks:
Oil life extended by 2x, reducing the frequency of oil changes
Maintenance costs reduced by 30%
Reduced production delays and inefficiencies within 2-3 months
Conclusion: The Experience of Owning VDS
The plant now runs with improved uptime, longer-lasting oil, and reduced wear on critical components.
The officials at the plant mentioned "Installing the VDS wasn’t just a technical upgrade, it completely changed how we think about oil maintenance. And honestly, it paid for itself in just three months"
Liasotech VDS isn’t just a filtration system, it’s a solution that helps plants control costs, improve reliability, and protect their bottom line.
If you’re facing similar challenges, don’t wait for things to escalate, invest in a cost-effective solution before it’s too late, Contact us on 7643993545 today!