You can see the oil samples and online particle count readings below:
Before Filtration After Filtration Initial Reading Final Reading
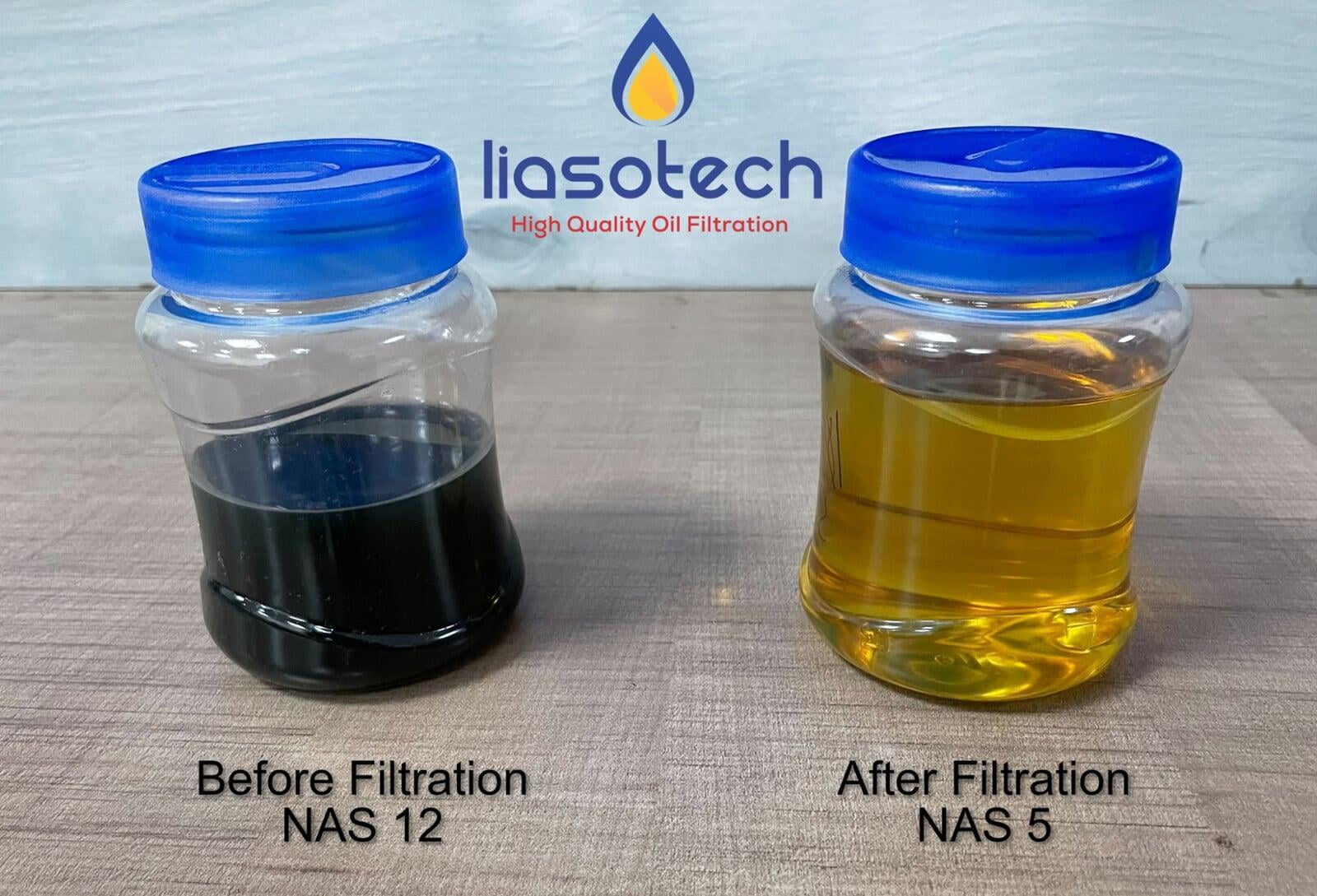
Liasotech conducted a successful oil cleaning demonstration at one of our customer's sites in the Plastic industry. This demonstration was crucial for the customer, who had previously faced multiple failures with other filtration companies in their attempts to clean hydraulic oil to the required standards.
Problem
Upon initial assessment, the hydraulic oil was tested and found to have a cleanliness level of NAS >12. This was significantly higher than the system's requirement of NAS 5. The excessive contamination in the hydraulic oil posed a serious risk to the machinery's performance and longevity, necessitating immediate and effective intervention.
Solution
In response to the customer's challenge, Liasotech deployed a skilled service engineer to the site for an initial assessment. Upon testing, it was confirmed that the hydraulic oil's cleanliness level was indeed at NAS 12. To address this, we installed a 12 LPM oil filtration machine equipped with 3-micron filters, all under the supervision of our service engineer. The filtration process commenced and continued non-stop for approximately 48 hours.
Result
The outcome of our intervention was highly successful. The filtration system reduced the oil's cleanliness level from NAS 12 to the desired NAS 5, meeting the stringent requirements of the customer's molding equipment. This significant improvement demonstrated the effectiveness of Liasotech’s technology and expertise in oil filtration.
Benefits
The successful filtration of the hydraulic oil brought multiple benefits to the customer. Firstly, achieving NAS 5 ensured the optimal performance and longevity of their equipment, reducing the risk of breakdowns and maintenance costs. Secondly, the customer, impressed by the results, expressed their interest in placing more orders. This not only solved their immediate problem but also paved the way for a long-term partnership with Liasotech, ensuring sustained equipment efficiency and reliability.
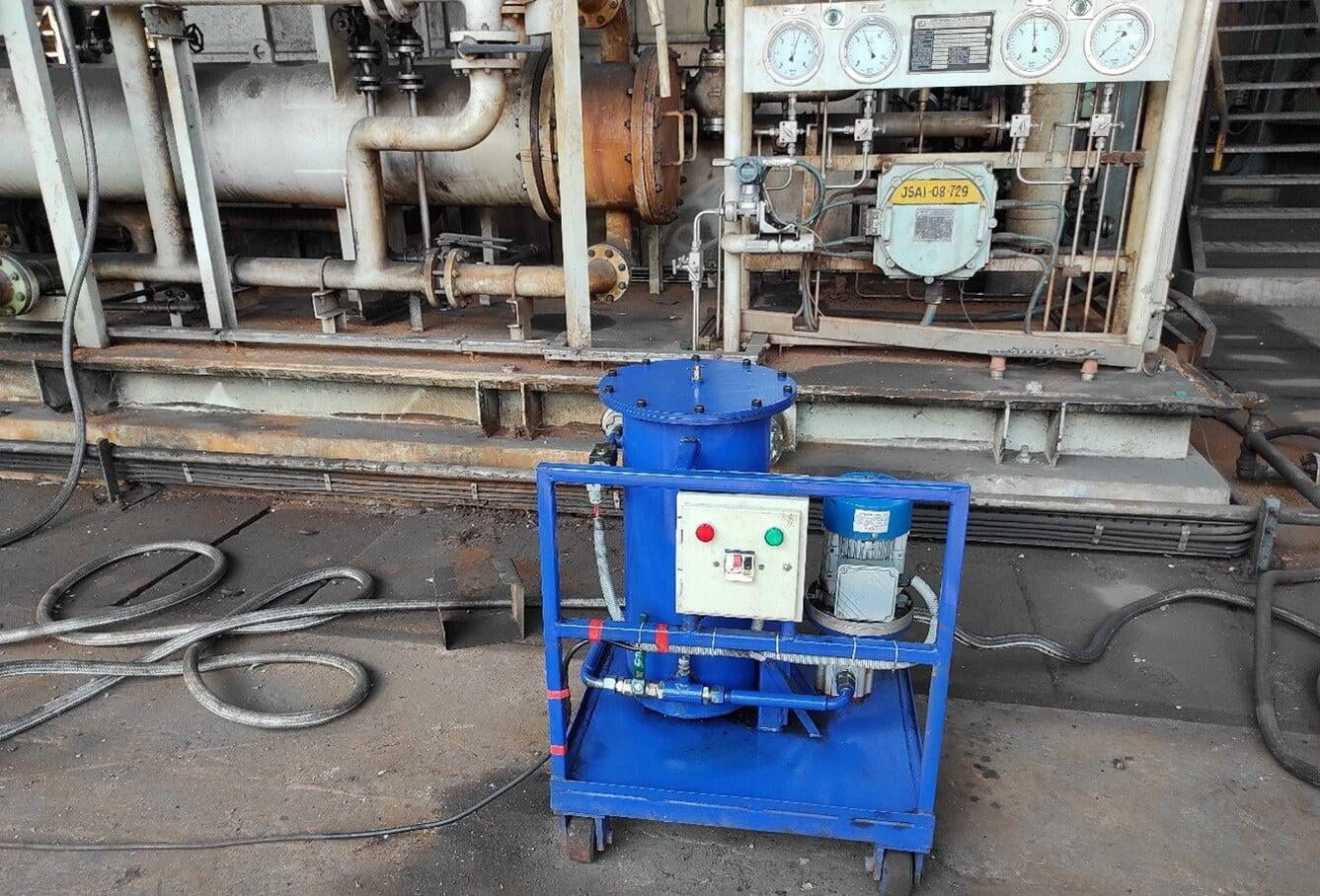
The Problem
An integrated steel plant in Odisha faced a significant challenge in maintaining oil cleanliness within one of its hydraulic systems, which has a 3000 liter tank capacity. Despite operating an ELC filtration machine continuously 24/7, the plant consistently recorded high particle count readings at NAS 10 or higher. Such high contamination levels posed a risk to the efficiency and longevity of the hydraulic system, making it critical to find a more effective solution to ensure system reliability and performance.
The Solution
To address the contamination issue, the plant official decided to replace the ELC filtration machine with our Hydraulic Oil Filtration System (HOFS-16). The HOFS-16 system was equipped with our finest 3-micron absolute filter elements, specifically chosen to eliminate particulate contamination in the hydraulic system effectively.
The Results
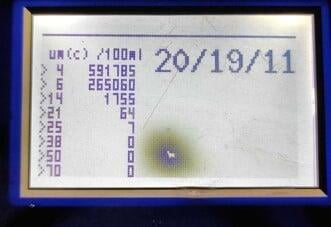
Initial Particle Count Reading - 09:30AM
The initial measurement taken at 9:30 am showed a particle count of 20/19/11, equivalent to NAS Class 10. This level of contamination was considerably high and unsuitable for the hydraulic system's optimal performance.
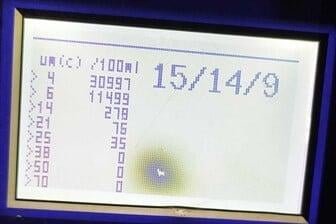
Final Particle Count Reading - 05:30PM
After operating the HOFS-16 filtration system throughout the day, a subsequent particle count reading was taken at 5:30 pm. The reading showed a significantly reduced particle count of 15/14/09, equivalent to NAS Class 5. This indicated a much cleaner state of the hydraulic oil, well within acceptable levels for such systems.
The Benefits:
Implementing the HOFS-16 filtration system brought several advantages:
The significant reduction in particulate contamination improved the hydraulic system's reliability and operational efficiency.
Cleaner oil helps reduce wear and tear on system components, extending their lifespan.
With lower contamination levels, the frequency of maintenance and associated downtime decreases, leading to cost savings.
Maintaining cleaner oil enhances the overall performance of the hydraulic system, contributing to smoother operations and improved productivity for the steel plant.
Problem Statement:
A cement plant in Andhra Pradesh had invested on an industrial oil filtration system from another manufacturer. Despite the cost and claimed benefits, they continued to face:
Failure to achieve the target NAS 5 cleanliness level, even after months of use.
Increased maintenance issues with hydraulic and lubrication systems.
Frequent machine downtimes and repairs.
This caused concern among the maintenance and operations teams, who had anticipated improved performance and cost efficiency.
Solution:
After understanding the challenges, we recommended our Advanced Oil Filtration System, designed specifically for critical equipment in dust-prone, high-temperature industries like cement.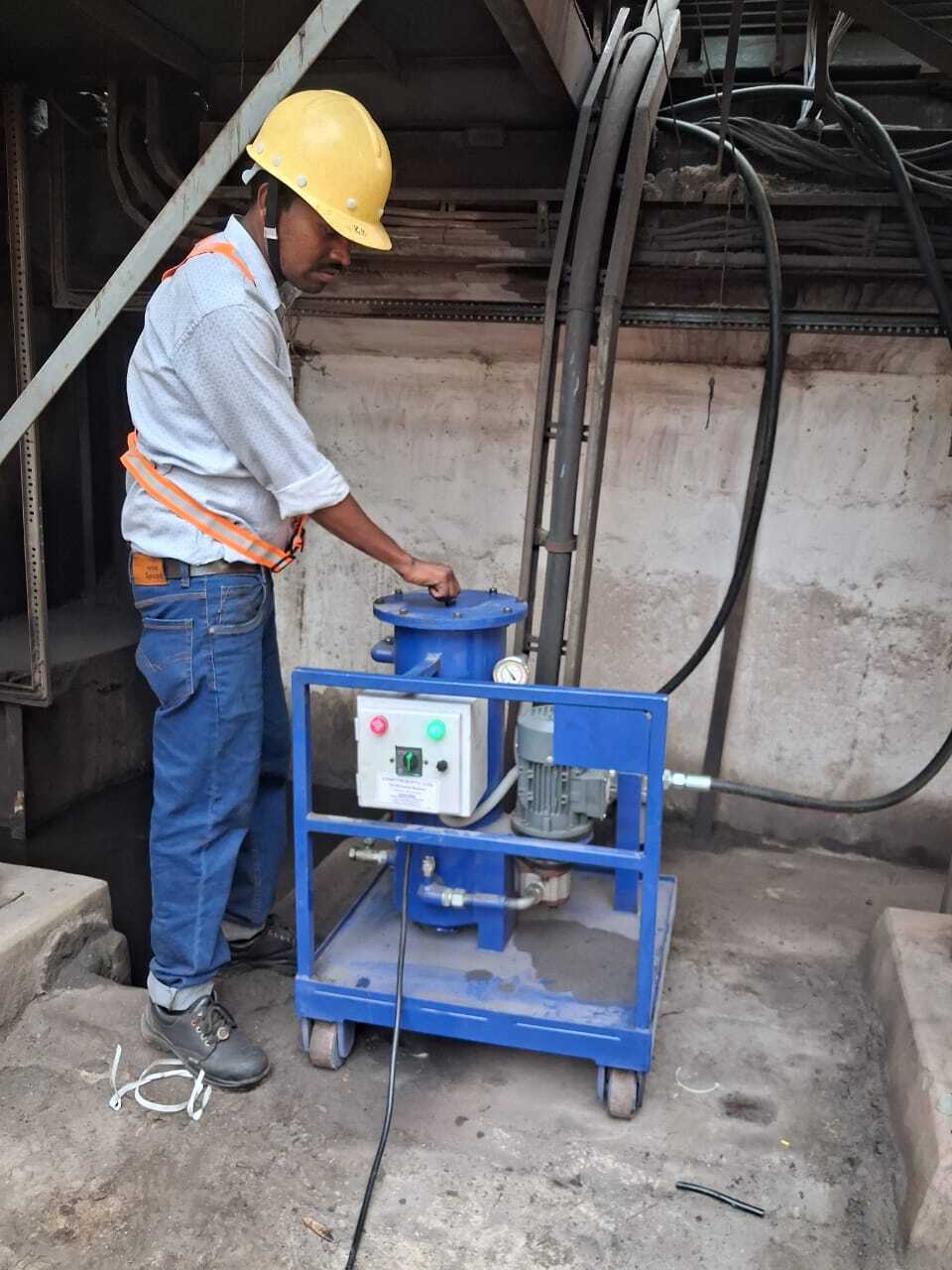
Implementation Highlights:
Installed a customized filtration unit compatible with their systems.
Provided on-site technical support for installation and training.
Ran continuous filtration in offline mode, allowing uninterrupted plant operation.
Started regular oil analysis to track progress.
Results
Within a short time frame of 48 hours of continuous filtration, the results were clear:
Oil cleanliness improved from NAS 11 to NAS 4
No replacement of oil was required, which helped them recover losses from their earlier investment.
The maintenance team reported noticeable improvement in equipment reliability and smoother operation.
Benefits:
a) Achieved NAS 5 Cleanliness, improving oil and machine health.
b) Reduced Maintenance Costs: Less component wear and longer oil life.
c) Avoided Costly Oil Replacement.
d)️ Enhanced Machine Uptime in a harsh cement plant environment.
e) Restored Trust in oil filtration solutions after a disappointing experience with a prior vendor.
The Problem
A ductile iron pipe manufacturer in West Bengal faced a serious challenge in their plant's hydraulic system.
The plant had already invested in a few number of oil filtration machines. But within just a few months, the Filtration Systems became ineffective, failing to deliver results. Concerned, they began searching for alternatives and that’s when they discovered Liasotech’s hydraulic oil filtration solutions through our website.
When we engaged with their maintenance team and reviewed their oil analysis reports, the root cause became clear:
Oil contamination ranging from NAS 9-12 in various systems, far above acceptable safety limits.
The plant officials explained that:
- Valves in the hydraulic presses were choked frequently.
- Movements became erratic : too slow, too fast, or stuck halfway.
- On the finishing tables, pipes were getting damaged due to delayed valve responses.
Machine cycles were becoming inconsistent, creating production losses and quality concerns
The Solution
Liasotech Oil Filtration System was then connected to their hydraulic press setup and the first baseline NAS reading was recorded: NAS 10.
We ran continuous offline filtration for 12-14 hours. Once the cycle completed, the new oil report showed: Solid contamination reduced to NAS 5
The Final Verdict:
Problem: Moisture Contamination issue in a Power Generation Company in Gujarat
A leading power plant in Gujarat was facing recurring challenges due to moisture contamination in their hydraulic systems. Despite routine maintenance, they experienced:
Hydraulic failures that delayed production and delivery timelines.
System inefficiencies due to reduced lubrication properties
The operations manager noted,
“Even with regular filtration, we couldn’t remove the dissolved moisture and we kept seeing equipment wear.”
Solution: Deploying Liasotech's Vacuum Dehydrator System (VDS)
While exploring advanced solutions, the team discovered Liasotech’s Vacuum Dehydration System (VDS) :: a system specifically engineered to remove free, emulsified, and dissolved water from hydraulic oils.
After installation, the results were immediate and measurable for 2 systems:
Mill | Oil Quality before VDS machine installation | VDS Installation Date & Time | VDS Machine Removal Date & Time | Total Time taken for moisture removal | Final Oil Quality |
A | Moisture – 600 PPM | 26.03.25 | 28.03.25 | 34 hours | Moisture – 90 PPM |
B | Moisture – 157 PPM | 04.04.25 | 05.04.25 | 18 hours | Moisture – 87 PPM |
In a few weeks:
Oil life extended by 2x, reducing the frequency of oil changes
Maintenance costs reduced by 30%
Reduced production delays and inefficiencies within 2-3 months
Conclusion: The Experience of Owning VDS
The plant now runs with improved uptime, longer-lasting oil, and reduced wear on critical components.
The officials at the plant mentioned "Installing the VDS wasn’t just a technical upgrade, it completely changed how we think about oil maintenance. And honestly, it paid for itself in just three months"
Liasotech VDS isn’t just a filtration system, it’s a solution that helps plants control costs, improve reliability, and protect their bottom line.
If you’re facing similar challenges, don’t wait for things to escalate, invest in a cost-effective solution before it’s too late, Contact us on 7643993545 today!This contamination led to excessive wear on bearings and gear teeth, causing oil seals to break frequently and resulting in severe oil leakages. The frequent breakdown of seals and leakages forced the plant to top up large amounts of fresh oil, increasing the consumption of Gear Oil.
The system continuously removes fine particles, metal debris, and moisture from the gear oil, ensuring it stays clean and within optimal operating conditions.
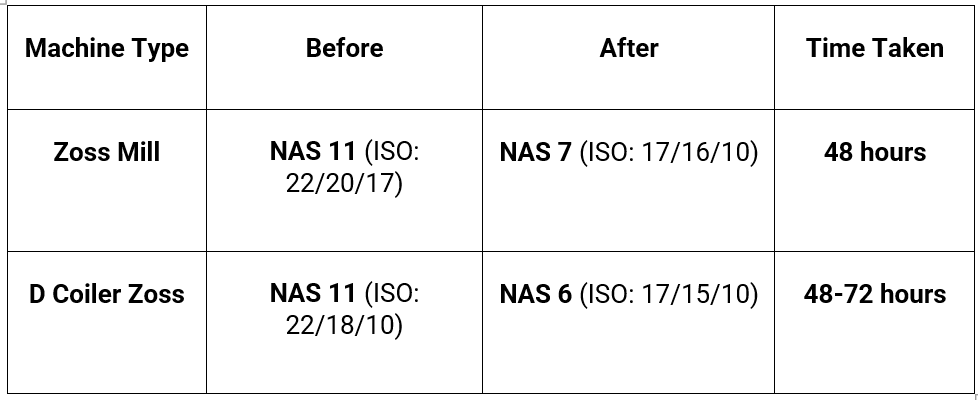
By maintaining oil cleanliness, the system prevents abrasive wear that breaks oil seals and causes leakages.
Engineered for dusty and high-load environments, Liasotech’s filtration solution operates continuously without interrupting production.
Result
After implementing Liasotech’s Gear Oil Filtration System, the steel plant experienced:
A dramatic drop in unexpected gearbox failures and unscheduled breakdowns.
Significantly fewer oil leakages and seal breakages, extending the life of oil seals.
Substantial savings on oil consumption costs due to reduced oil top-ups.
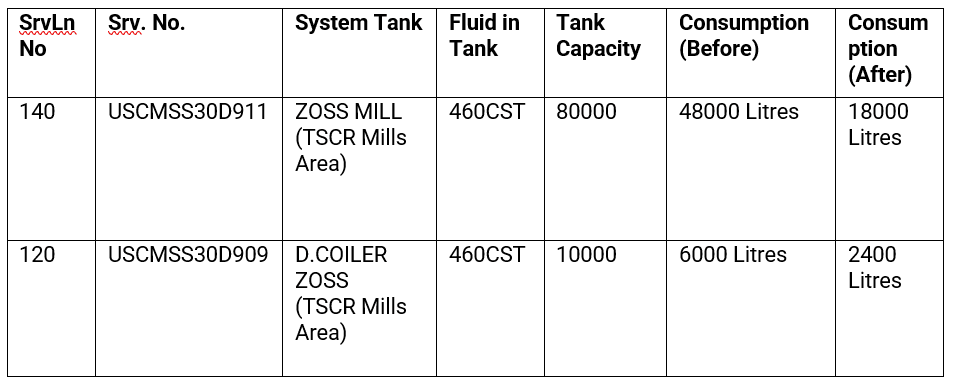
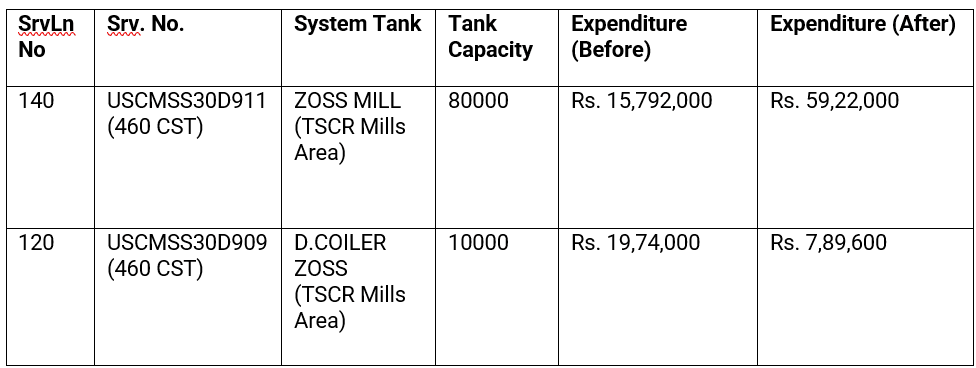
- Improved gearbox performance, with overheating and friction issues largely eliminated.
- A shift from emergency repairs to planned, predictive maintenance, boosting overall reliability and productivity.
Key Takeaway
A prominent automotive parts manufacturer in Maharashtra, supplying parts to various OEMs relied on high-capital CNC machining lines for precision components. These lines are the backbone of their production and demand uninterrupted performance to meet tight delivery schedules and maintain product quality.
Frequent unplanned stoppages of critical machining lines.
Rapid degradation of key components such as bearings, spindles etc.
Fine metal particles generated during machining were not being removed effectively by inline filters.
Fresh lube oil consumption was rising 20% above normal levels, adding to operational costs.
These issues posed a serious threat to their high-value capex machinery, risking expensive repairs, unscheduled downtime, and loss of production hours.
Continuously remove fine solid particles down to 3 microns.
Extend oil life by maintaining consistent cleanliness and moisture control.
• (NAS) cleanliness: NAS 11 to NAS 5.
The NAS 5 cleanliness level was achieved after filtering 1,000 litres of contaminated oil for 10 hours.
- Oil Change Frequency: From every 4 - 12 months
- Unplanned Downtime: Reduced by 70%
- Annual Savings Achieved:
- Fresh oil cost savings- 50%
- Downtime cost savings: 45%
Key Benefits Delivered
- Protected high-value capex machinery from wear, rust, and unplanned failures.
- Improved oil life by 3x, reducing waste and environmental impact.
- Reduced maintenance interventions, freeing manpower for more productive tasks.
- Enhanced overall production reliability, safeguarding delivery timelines.
Problem:
A chemical and fertilizer manufacturing plant faced major issues with its lube oil due to contamination:
Water ingress & emulsified lube oil: Water levels exceeded 1,000 PPM, causing emulsification.
High particle contamination: Particles lead to wear on bearings. The particle counter machine showed ISO- 21/19/14 or NAS 10.
Frequent oil changes & valve failures: Oil changed every 3–4 months instead of 12, leading to hydraulic system valves failing every 5 months.
Annual loss: Estimated ₹13–15 lakh due to maintenance, oil changes, and downtime.
Solution:
The plant installed 6 nos of Lube Oil Filtration System for removal of particle contamination and 1 no of Vacuum Dehydration System for water removal. Following steps were implemented as follows:
Installing Lube Oil Filtration System to remove particles with β3 ≥ 500 rating.
Vacuum Dehydrator Filtration System to eliminate free and dissolved water.
Regular Filtration: The process began by removing moisture over a 48-hour period, after which dedicated filtration machines were installed and operated for one week.
Oil Monitoring: Oil testing was done on scheduled interval to check moisture and cleanliness levels.
Results (10 Days Later):
- Water Content: Reduced from 1,000+ ppm to <100 ppm.
- Particle Cleanliness: Improved from 21/19/14 (NAS 10) to 16/13/9 (NAS 5)
- Oil Change Frequency: Increased to every 15-16 months
- Valve Failures/Choking : No breakdown in 12 months since it's date of installation.
- Manual Water Drain: Eliminated.
- Annual Savings: ₹9–11 lakh.
Conclusion:
The Moisture contamination reduced from 150PPM operating at an efficiency of 68% to 60PPM and improved the efficiency to 74%. This improvement not only enhances operational reliability but also supports sustainability by reducing energy wastage, extending oil life, and lowering the environmental impact of frequent oil replacements.
Conclusion:
Implementing our industrial oil filtration system significantly improved turbine performance, reduced downtime, and lowered maintenance costs for the company's power plant in Karnataka.