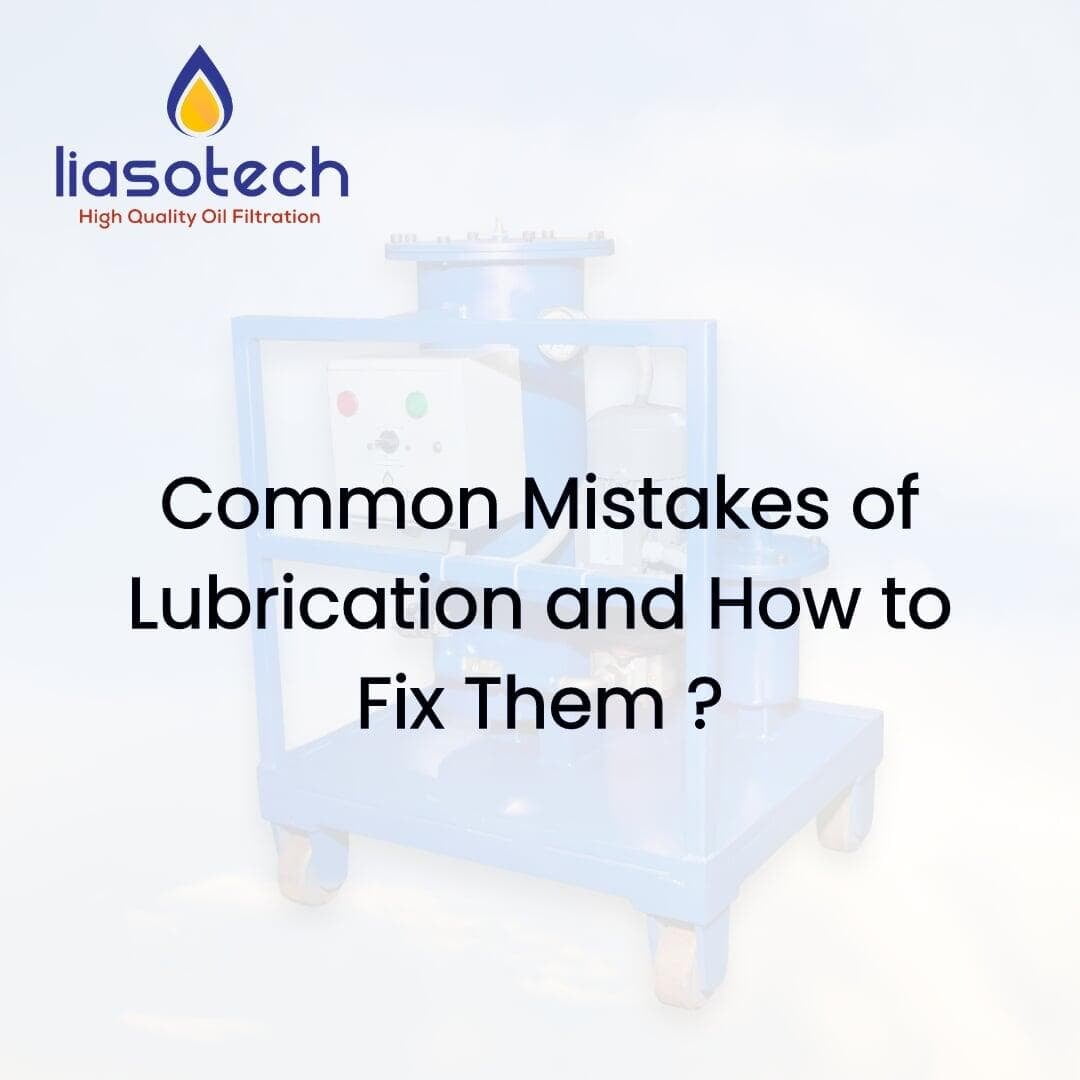
Neglecting Regular Lubrication Checks:
Failing to maintain a regular lubrication schedule is a common mistake. Consistent lubrication reduces friction and prevents wear. Without routine checks, lubricant levels can drop, causing increased friction, overheating, and component failure. Implementing scheduled lubrication intervals can mitigate this risk.
Incorrect Lubricant Selection:
Using the wrong lubricant can lead to poor lubrication, reduced performance. It's crucial to select the correct lubricant based on equipment manuals and industry standards, considering factors like operating temperature, load, and speed.
Over-Lubrication or Under-Lubrication:
Balancing lubrication quantity is essential. Over-lubrication can cause high temperatures, energy wastage, and leakage, while under-lubrication can lead to friction and wear. Proper procedures, automated systems, and regular oil analysis can help maintain optimal lubricant levels.
Poor Lubricant Storage and Handling:
Improper storage and handling can degrade lubricants. They should be kept in clean, sealed containers away from contaminants, moisture, and extreme temperatures. Clean equipment and proper handling practices during lubrication are also crucial.
Ignoring Lubricant Condition Monitoring:
Monitoring lubricant conditions helps identify issues early. Lubricants degrade over time due to contamination, oxidation, or additive depletion. Regular oil analysis can detect abnormalities, allowing for timely maintenance and preventing breakdowns.
Lack of Training and Documentation:
Regularly monitor lubricant condition to detect issues early. Oil analysis can identify abnormalities like increased wear metals, water content, or viscosity changes, allowing for timely maintenance and preventing breakdowns.
In conclusion, avoiding common lubrication mistakes is key to maximizing equipment reliability, efficiency, and lifespan. By implementing proactive maintenance, choosing the right lubricants, maintaining optimal levels, and monitoring conditions, organizations can reduce downtime, cut maintenance costs, and improve operational performance.