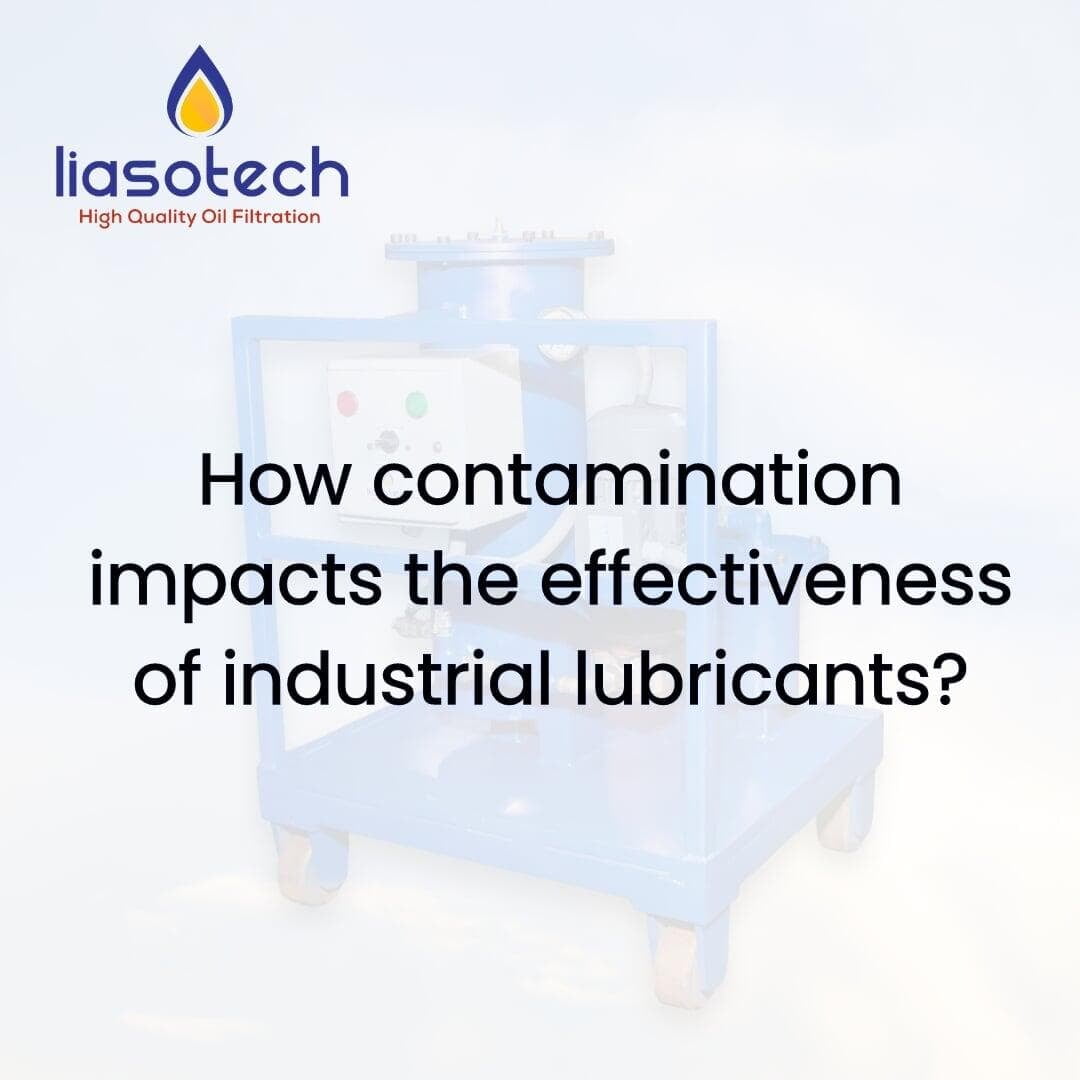
Industrial lubricants are vital for machinery in sectors from manufacturing plants to automotive workshops. They reduce friction, minimize wear, and enhance efficiency. However, contamination can significantly reduce their effectiveness. Understanding the impact of contamination is crucial for maintaining machinery performance and preventing costly downtime.
Types of Contaminants
Contaminants in industrial lubricants are solid, liquid, or gaseous. Solid contaminants include dirt, metal particles, and wear debris. Liquid contaminants are usually water or other incompatible fluids, while gaseous contaminants are air or other gases.
Sources of Contamination
Contamination can arise from multiple sources, such as unsealed storage containers, worn seals, open ports, and the external environment. Poor handling and dispensing methods also introduce particles into lubricants.
Impact on Lubricant Performance
Reduced lubrication efficiency: When contaminants infiltrate lubricants, they can disrupt their viscosity, essential for upholding a protective barrier between surfaces. Fluctuations in viscosity may result in insufficient lubrication, enhanced friction, and accelerated wear.
Increased wear and tear: Contaminants alter the lubricant's viscosity, compromising its ability to create a protective layer between moving parts. This weakens the film strength, leading to increased friction and heat generation, which can escalate wear and potentially cause equipment failure.
Corrosion and rust: Water and chemical contaminants can initiate and accelerate corrosion processes, particularly in ferrous metals. Corrosion weakens structural integrity and can lead to component failure if not addressed promptly.
Oxidation and degradation: Chemical contaminants and water can promote oxidation of the lubricant, forming acids and sludge. This degradation affects the lubricant's ability to protect surfaces, resulting in increased maintenance costs and reduced operational efficiency.
Thermal issues: When lubricants are contaminated, they struggle to disperse heat efficiently. This gradual buildup can cause overheating further accelerating lubricant breakdown and increasing the risk of thermal damage to components.
Prevention and Control:
Regular Monitoring and Testing: Implementing a routine schedule for lubricant analysis helps in the early detection of contaminants. Testing can identify changes in viscosity, presence of water, particulate levels, and chemical contamination.
Proper Storage and Handling: Lubricants should be stored in clean, sealed containers away from potential contaminants. During handling, use clean equipment and maintain proper sealing to prevent ingress of dust and moisture.
Effective sealing systems: Ensure that machinery seals are intact and functioning properly to prevent the ingress of contaminants. Breathers and filters should be regularly checked and replaced as necessary.
Filtration systems: Incorporate advanced filtration systems in machinery to continuously remove particulates and water from lubricants, maintaining their purity and effectiveness.