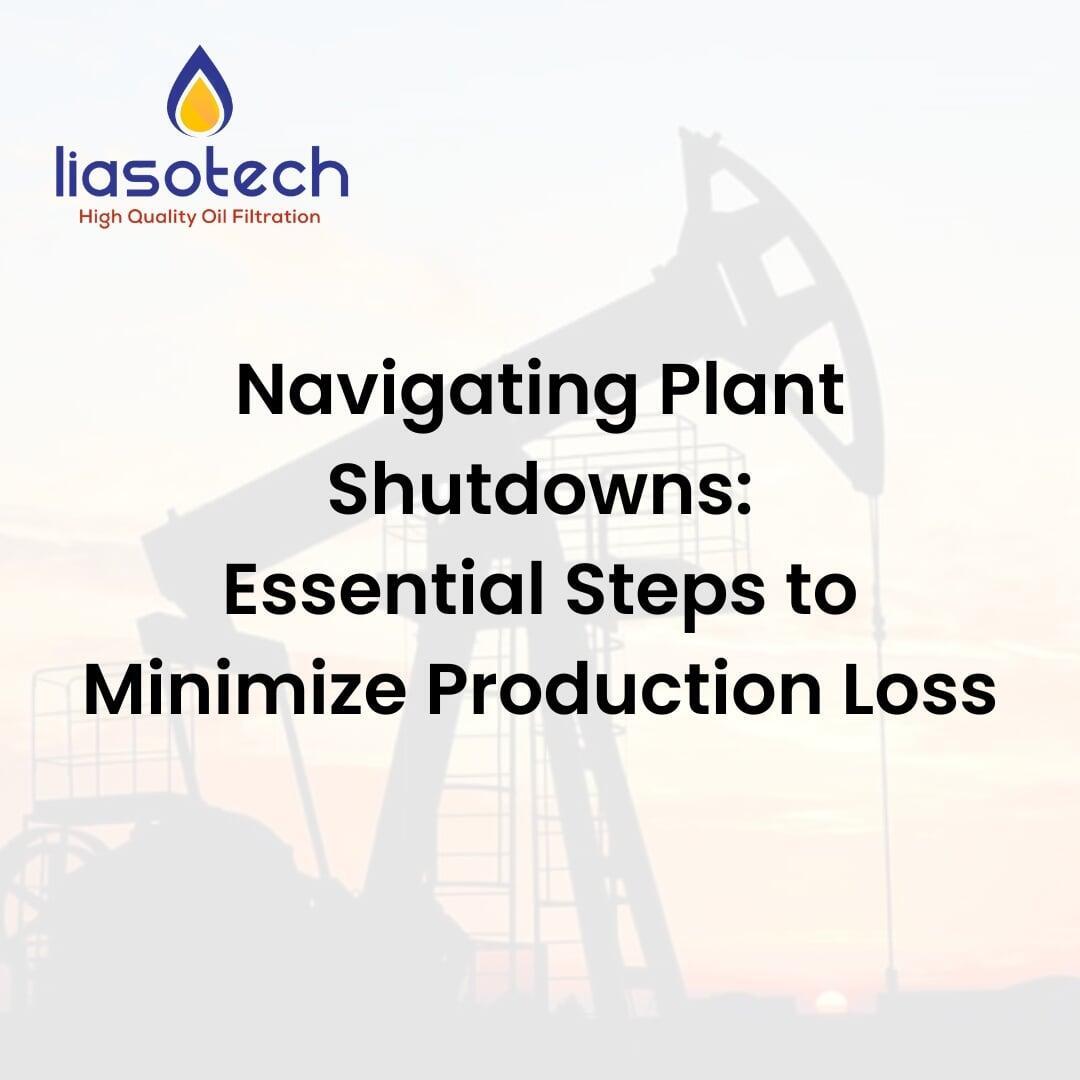
Plant shutdowns, whether planned or unexpected, can lead to significant production losses and financial strain. However, with the right approach, these challenges can be minimized. Here are key steps to navigate plant shutdowns effectively:
Proactive Planning
Start with a comprehensive shutdown plan well in advance. Identify critical equipment, scheduled maintenance, and potential risks. Ensuring a detailed timeline for each task can prevent unnecessary delays.
Clear Communication
Maintain open lines of communication across all teams—engineering, operations, safety, and maintenance. A well-informed team is better prepared to handle challenges promptly.
Preventive Maintenance
Take advantage of downtime for preventive maintenance. Addressing minor issues before they become major problems can prevent future shutdowns and extend equipment life.
Staff Training & Readiness
Ensure staff is trained to handle shutdown scenarios and emergency situations. Cross-train employees to cover multiple roles to avoid labor shortages during critical phases.
Supply Chain Coordination
Coordinate with suppliers to ensure that parts and materials are available ahead of time. Avoid delays in critical inventory by securing resources early.
Post-Shutdown Analysis
After restarting operations, conduct a post-shutdown review. Identify what went well and areas for improvement to streamline future shutdown processes.
By integrating these essential steps, plants can mitigate risks and ensure a smoother, more efficient shutdown, ultimately minimizing production losses.